Tank cleaning
It is customary to clean the cargo tanks as a preparation to load the next cargo after the cargo is discharged and the tanker sails out from the discharge port. This is done because the next cargo may not be compatible with the earlier cargo or the vessels cargo tanks may have to be entered for maintenance / inspection or the vessel needs to be prepared for dry docking or lay up.
Crude oil washing (COW)
Crude oil washing uses the cargo itself to wash the tanks. The cargo oil is injected in the tank under pressure which emulsifies the clingage and allows the oil to be pumped out with the least amount of sludge etc,
With stringent MARPOL regulations in force, the tank cleaning is kept to a minimum. On a crude oil tanker, during discharge, 25% of the tanks should be washed on a rotational basis so that all the tanks are washed at least once every four months.
This is done to eliminate the amount of oil entering the sea through the tank cleaning process and for controlling the build up of sludge in the tanks.
Aim of COW
Crude oil washing of the tanks aims at:
- Reducing the amount of cargo left in the tank after discharge,
- Removing the sediments, waxes, sand, etc. in the oil, which tend to settle on the ships structure in the tanks and keep accumulating up over a period of time. When this build-up of sediments is not attended to, the net cargo carried decreases and the vessel’s efficiency in terms of cargo carried, deteriorates.
- Consequently, increase the quantity of cargo carried
The COW system
The system consists of
- A set of fixed tank washing machines in each cargo tank.
- Each machine has its own isolation valve on deck.
- Pipelines connecting each machine to the main COW line are permanently fitted.
- Main COW valve(s) connects the discharge of the cargo pump(s) to the main COW line(s).
The cargo from the main cargo line is pumped at a pressure and supplied to the main COW pipelines controlled by a main isolation valve(s). The main COW pipeline(s) are further branched off and connected to each of the COW machines having their own isolation valves. These machines are permanently fitted inside cargo tanks at strategic locations.
At the end of the machine are nozzles, which force the cargo into a jet, which impinge the insides of a cargo tank. The nozzles are made to move in azimuth (0° to 360°) and in elevation (bottom – 0° to top – 180°) giving the jet of cargo a helical motion, which helps in cleaning the entire tank effectively.
This movement of nozzle (in azimuth and elevation) are achieved using either a compressed air motor or with help of turbine using the flow of oil itself through the machine. Further more the machines could be of programmable or non-programmable type. In the programmable type it is possible to programme and set the nozzle to “cycle” between any two elevations. In the non-programmable type the nozzle keeps cycling between bottom (0°) and top (180°). The rotation in azimuth is however uncontrollable in both the types of machines.
Typical wash cycles are bottom wash (0° to 50°), middle wash (50° to 90°) and top wash (90° to 180°).
The procedure
A great deal of planning needs to be made before a COW can be undertaken.
Preparations include:
- Debottoming of all the tanks.
- Priority to discharge all the identified tanks, which needs to be crude oil, washed.
- Identifying the tank in which the initial charge of crude oil can be taken. Empty slop tanks may also be considered for taking this initial charge.
- Understanding the limitation of the ships piping system that the taking a charge of cargo in a separate tank, crude oil washing and continuous stripping of the selected tanks can severely affect the discharge performance of the vessel.
Most vessels undertake a closed cycle COW method. This means that the ship uses one of its cargo pumps to feed the cargo from the initially charged tank to the COW machines of the tank being cleaned. The same pump also drives the eductor to keep the bottom of the tank being cleaned, stripped dry, especially for the bottom wash. The eductor discharges the drive liquid which now includes the cargo, sediments and wax from the tanks being cleaned into the tank containing the initial charge. This liquid needs to be discharged ashore and the tank has to be recharged with fresh dry crude before washing more tanks. The tank is required to be periodically discharged ashore and level monitored continuously to prevent it from overflowing during the COW process, especially when a small tank like a slop tank is used.
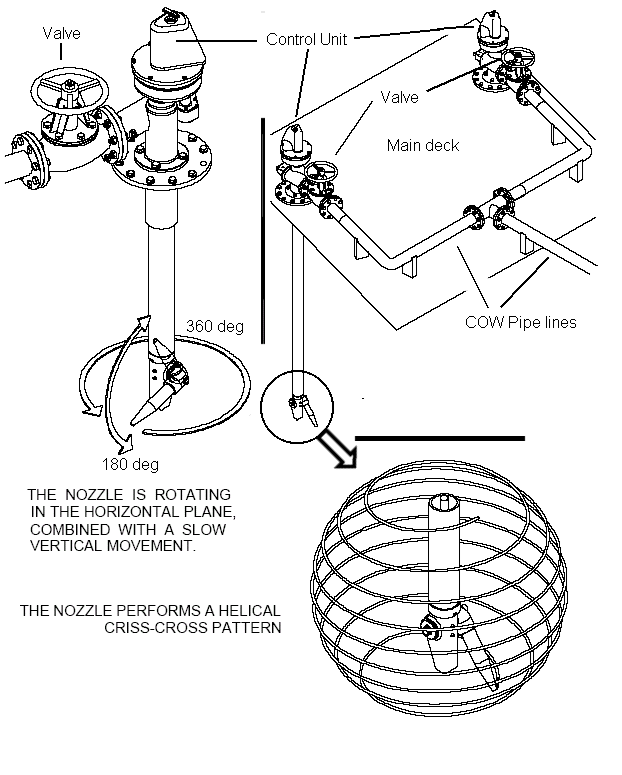
Fig: Control unit with valve, under deck nozzle of a COW machine and the general layout of the COW system on a tanker (note the helical pattern made by the moving nozzle of a COW machine inside the tank
Preparation of tanks for COW
After making the prescribed checks in the tank, the valves of the individual COW machines, for the tank to be washed, are opened. It is a good practise to ensure that all other valves, not in use, are kept closed. The COW line main valve is opened and the cargo is diverted to the COW line. After checking that there are no leaks in the line and that cargo is reaching the machines to be used, the pressure on the COW line is increased slowly to the max working pressure. The stripping of the tank is continued throughout the COW process.
The crude oil, which is delivered under pressure, impinges on the ship’s structure thereby dissolving the sediments and waxes and dislodging the sand and other deposits and carrying them to the pump suction for discharge ashore via the slop tanks.
Crude oil washing is a hazardous operation because when the crude oil passes through the nozzle of the machine, there is a build up of static charge in the pipe line and in the atmosphere in the tank. The COW line flanges are therefore bonded with a strip of metal (This is called bonding) to make the pipeline electrically continuous for the static charge to dissipate to the ships structure. In the tank, there is a build up of static charge in the form of a vapour cloud. This could cause a spark if the charge is allowed to jump across onto an object which does not have charge or which is at a lower or opposite potential than that of the charged cloud. If there is water in the crude oil used for COW then the presence of static cloud will be very prominent.
These problems are overcome by carrying out the following operations:
De-bottoming of the cargo tanks
After a long voyage when the tanker comes into discharge port and it is intended to carry out COW, all the cargo tanks are de bottomed, i.e. on commencement of discharge all the tanks are discharged to increase their ullage by 1m. This is done because during the voyage, all the water in the cargo settles to the bottom. Since suction is taken from the bottom & if 1 m cargo is discharged, we can safely say that all the water at the bottom of the tank has been discharged. Thus at a later stage if any of the cargo is used for COW there will be no water in the cargo.
Controlling tank atmosphere
Before starting COW operation of any tank, check that the tank atmosphere is at least at 100mm WG (water gauge) (Preferably 400mm WG) above atmospheric pressure and the oxygen content should not be above 5%. A tank in which COW operation is being carried out should not be isolated from the IG system as any leakage will allow the pressure to drop and then outside air could get into the tank.
Introduction of foreign objects into the tanks
Before starting COW in a tank, all external equipment introduced into the tank should be withdrawn and the float gauges should be wound up. This will prevent them from getting damaged. During COW operation no object should be introduced into the tank and at least 30 minutes decay period should be allowed after completion of COW operation before any sounding tape etc. can be introduced into the tank. It is assumed that the static charge build-up in the tank atmosphere will dissipate to the surrounding structure in 30 minutes. After 30 minutes, objects may be introduced into the tank but it is always good practise to earth the equipment before introducing it into the tank.
For effective COW, the operation should be commenced when there is about 30 cms of cargo in the tank and the pressure on the COW line should be at least 8 kg/cm2 or as specified in the COW manual on board. The stripping system should be efficient and by the time the COW operation is complete, the tank should be stripped dry. As there is no manual means of checking the efficiency of the stripping while the COW operation is going on, eductors are used, since their performance is not affected even if they draw gas. In the figure below, the wash pattern of two machines is shown on one side each. In actual practise the machine cleans in all directions by rotating through 360º.
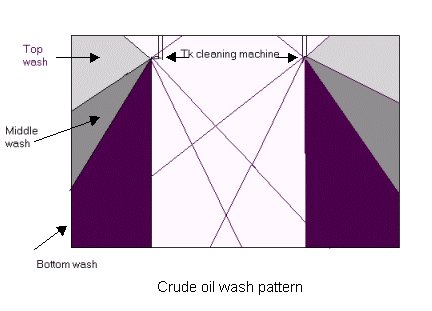
The angle of the top wash, middle wash and bottom wash are as per the COW manual on board. In case of non-programmable machines, where the angle of wash cannot be controlled, the time duration for the washing operation is decided by the time required to complete one cycle of wash. The instruction manual for the machine gives the time duration of one full cycle.
Normally all charter parties under which crude oil is carried, allow 6 hours extra time at berth to carry out COW operation. The time allowed for each tank is decided by referring to the ship’s COW manual and from past experience. It should be borne in mind that COW cannot be done with all crude oils and hence the material data sheet should be referred to or instructions sought from owners or charterers.
Precautions to be taken before, while and after COW
- Port authorities need prior intimation on the ships intension to carry out COW.
- De bottom all the tanks and discharge slop tanks completely and recharge with dry crude.
- Check lists as given in ISGOTT to be completed before starting COW.
- Before commencing COW:
- ensure that the oxygen content in the tank is less than 5%,
- the pressure of IG should be above 100 mm WG (preferably 400 mm WG),
- the float type gauge to be wound up,
- the machines if programmable to be programmed to carry out top wash first,
- the stripping system to strip the tank while COW, to be checked for proper functioning,
- ensure that the COW valves of only those machines, which are going to be used, are open.
- As soon as cargo enters the COW line, check in pump room and on deck for leaks.
- Raise pressure on the COW line slowly, to the working pressure.
- An officer to be continuously on deck to monitor the COW operation, the pump room also to be manned during COW. If the stripped cargo is also being put into a tank, then the tank shall be checked to prevent overflow.
- Crew should not be allowed to carry keys, lighters, match boxes or any such items which may give rise to a spark, if they fall, or are misused.
- Effective deck watches to be maintained during the COW operation.
- On completion of COW, all the lines to be drained and the valves to be shut.
Water washing of tanks
Tanks are washed with water:
- If a cargo that cannot tolerate any remnants of the last cargo is to be loaded.
- For man entry
- Preparing a vessel for dry-docking
If the vessel is equipped with fixed machines then it is advisable to carry out the washing in a controlled atmosphere. If portable machines have to be used then the atmosphere cannot be controlled and hence it should be ensured that no source of ignition is allowed to come in the vicinity of the tank.
While water washing, a closed cycle is followed i.e. first the secondary slop is filled with seawater and this water is pumped with the cargo pumps into the tank washing line. A part of the discharge of the pump is diverted to the eductor as drive water and the eductor starts stripping the tank, which is being washed. The discharge from the eductors is taken to the primary slop tank. The primary slop has a means of decanting into the secondary slop
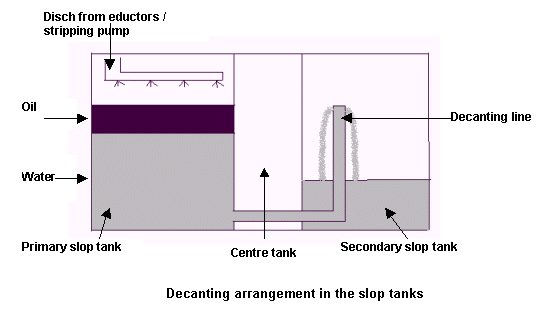
Primary slop tank is the slop tank into which the stripper pump / eductor discharge is received. Secondary slop is the slop from where the wash water is drawn for washing the tanks.
Decanting arrangement
The discharge from the eductors is sprayed into the tank (as shown in the figure) and this helps the oil and water to separate. As the level of water in the tank rises, the water rises into the decanting line also and once the level of water in the primary tank reaches the height of the opening of the decanting line, the water in the decanting line starts falling into the secondary slop tank. The secondary slop tank does not have any oil as the oil floats on top of the water and is retained in the primary slop tank. The pump draws this water from the secondary slop tank and puts it in the tank washing line. Thus at the end of the washing, all the oily water is in the primary slop tank. This water is allowed to decant for at least 24 hrs and then as per the provisions of MARPOL it may be discharged into the sea or to shore facilities. It is customary to determine the interface (the boundary between the two liquid which are of different densities) between the oil and water and then the water is disposed off within 1 m of the interface or when the quantity discharged exceeds the permissible limits, while discharging into the sea.
Ballasting and de ballasting
On SBT (segregated ballast tanks) tankers the ballasting / deballasting operations do not pose a problem. There is no danger of contamination of the ballast with oil because the ballast system and the cargo system are completely segregated and they can be connected, in an emergency, by inserting a spool piece in the pump room. (This spool piece is never to be kept inserted in its place but should be secured in a conspicuous place in the pump room for ready use). On a SBT tanker, this spool piece may have to be inserted if the vessel has to ballast the cargo tanks. It will be required to ballast the cargo tanks in case of heavy weather or in exceptional circumstances where the vessel may have to achieve a trim, which cannot be achieved by using the normal ballast tanks. In SBT tankers the ballast lines do not pass through the cargo tanks and the cargo lines do not pass through ballast tanks.
Ballast should be taken to meet air draft requirements on the berth, particularly when chicksans or rigid cargo arms are connected. Ballast may be restricted if it may cause the vessel to exceed the maximum safe draft for the berth.
Care should be taken when ballasting and deballasting that excessive free surface is not allowed to occur which may result in the vessel assuming an angle of loll, jeopardising the integrity of the loading arms. This is particularly relevant to double hull tankers.
The ballasting / discharge or deballasting / loading operations can be done simultaneously without any problems but the following must be kept in mind:
Loading and discharge of ballast should not cause extreme bending or shear forces on the vessel.
If deballasting of ballast tanks are carried out simultaneously with the loading procedure vapours may be emitted from the tanks being loaded. These vapours may be drawn into the ballast tanks, in which case proper precautions should be taken.
The use of an oil content monitor for monitoring the discharge of clean or segregated ballast will give an early warning of any undiscovered contaminated ballast caused by, for example, inter-tank leakage when loading and deballasting are being carried out simultaneously.
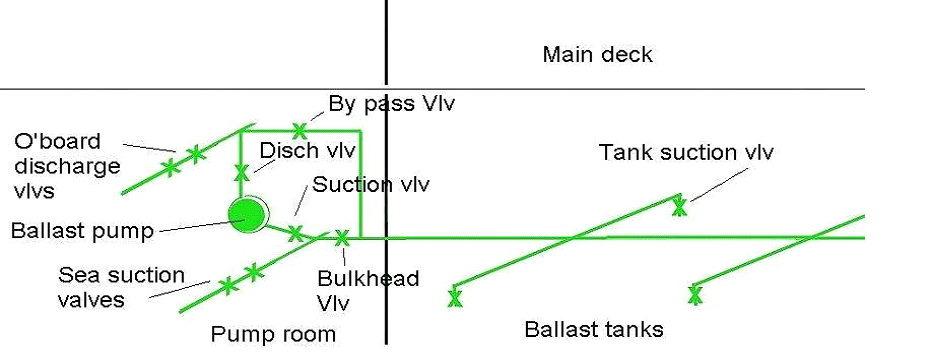
Fig: showing portion of the ballast tanks and all associated pipelines and valves
A typical ballast line arrangement can be seen in the above figure. The system of pipelines and valves enables the ballast tanks to be filled up or emptied either by gravity or by pump. Generally two ballast pumps are provided on a tanker to speed up the deballasting or ballasting process. Though not shown in the figure the sea chest line and the overboard valves are available on both the port and starboard sides. Filters and mud boxes are also provided after the sea chest valves to filter out the debris in order to avoid damage to the pump.
Before commencing deballasting, the surface of the ballast should be inspected to check that it is clean. In some ports ballast may be sampled and tested for contaminants before deballasting can commence.
On commencement of deballasting, a visual watch should be established to observe the ballast as it discharges into the sea. The operation should be stopped immediately in the event of contamination being observed.
Cargo loading and discharging
In the first year of your course you studied the fundamentals of various types on pipelines available on an oil tanker. The below describes a typical arrangement available on a product/crude oil tanker.
A typical loading and discharging system on an oil tanker consists of the following:
- Pipelines with valves on deck
- Pipelines with valves inside the tanks
- Pipelines with valves inside the cargo pump room
- Stripping system
These pipelines are arranged in groups with their own manifolds, cargo pumps, drop lines, lines in tanks, on deck and inside the pump room to enable simultaneous loading and discharging of different cargoes without contamination. These groups may be combined together using a system of crossovers on deck, inside the tank and in the pump room. Groups are numbered or colour coded for easy identification and reference.
Pipelines begin at the tank suction, pass through the cargo pump and rise up on the deck before ending up at the manifolds at each side of the ship where shore hoses or loading arms are connected for the cargoes to be loaded and discharged ashore.
Somewhere in between the pump room and manifold the pipe drops down into the tank and joins the tank suction line. These are the drop lines, which lead vertically down into the tanks and are usually meant for loading.
Normally four such sets of pipelines are available on an oil tanker which could be connected together with crossovers on deck, pump room and tank in order to have the flexibility to load and discharge different quantities of cargoes without contamination. Note the double valve crossover used when connecting the pipelines of two different groups.
Upon completion of the bulk discharge of the cargo using the high capacity main cargo pumps, the remaining cargo in the tanks and in the pipelines are removed using a small diameter line referred to as ‘stripping’. There are a number of such systems available.
Using a steam operated reciprocating stripping pump and a separate small diameter line (stripper line) for each group of tanks, each tank is provided with a small diameter suction pipe for stripping operation. The discharge from the stripper pump is connected to the main pipe line before the manifold.
Some ships use eductors instead of the stripper pumps. These systems use the liquid of the cargo pump as a drive and stripper lines as mentioned above to pump out the last bit of cargo on board.
Some ships however do not have a stripper pump but they have a system which uses a centrifugal pump, a small tank just before the suction of the main cargo pump and a vacuum pump connected to the small tank. Level sensors connected to the small tank start and stop the vacuum pump. The level sensors also control the main cargo pumps discharge valves automatically depending on the level of the oil in the small tanks.
A brief working of such a system is as follows:
The main pumps are discharging when the level of the tank is high. There is a fear of the pump losing suction as the level reduces.
When the cargo tank’s level goes down the level in the small tank also reduces and activates the vacuum pump and at the same time throttles the discharge valve of the centrifugal cargo pump.
This vacuum pump creates a vacuum in the small tank, which creates a suction effect. The oil from the cargo tank rushes into the small tank and the level in the small tank increases as a result of this.
Once the desired level is reached the vacuum pump cuts off and the discharge valve of the main pump opens fully increasing the cargo flow.
Should the sensors sense the low level in the small tank again, the vacuum pump cuts in and the discharge valve are throttled once again. This process is repeated until the entire cargo is pumped out. The centrifugal cargo pumps in this manner continue to pump out the liquid completely with out fear of losing suction.
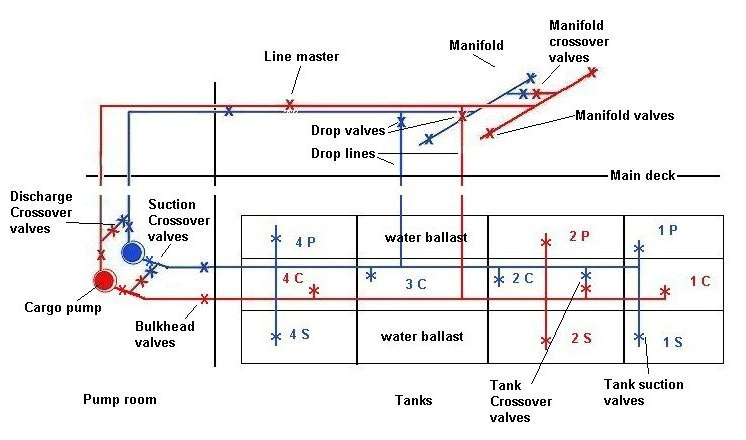
Fig: Typical pipe arrangement on a tanker designed to carry two parcels of cargo segregated with at last a double valve.
General precautions
All cargo operations must be carefully planned and documented well in advance of their execution. The details of the plans must be discussed with all personnel, both on the ship and at the terminal. Plans may need to be modified following consultation with the terminal and following changing circumstances, either onboard or ashore. Any changes must be formally recorded and brought to the attention of all personnel involved with the operation.
A written plan generally consists of details concerning:
- watch keeping schedules,
- pre operation checks,
- flow rates,
- limitations of the vessel / terminal, lining up,
- commencing the operation,
- monitoring the operation,
- ullage levels,
- tank changeover times,
- procedures,
- Stress / bending moments at various stages etc.
Protection alarms like overfill alarms must be tried out and tested prior commencement of loading.
Setting of lines and valves
Before commencement of any loading or discharging operation, the ship’s cargo pipelines and valves should be set as per the required loading plan by a responsible officer and checked, independently, by other personnel.
Setting up of lines should not pose any problem provided the officer consults the mimic diagrams and piping plans in a correct manner. He must check and double that the lines are set properly. A second check by another person must be carried out physically to ensure that the lines are set properly.
An open valve, which is supposed to be kept, shut and vice versa may lead to damage to ship, equipment and environment.
Loading through pump room lines
Due to the increased risk of leakage in the pump room, it is not a good practice to load cargo via pump room lines. Cargo should be loaded through drop lines within the cargo tank area, with all pump room valves closed.
General loading procedures
The responsibility for safe cargo handling operations is shared between the ship and the terminal. Sharing the responsibility must be agreed by each so as to ensure that all aspects of the operations are covered.
Readiness to load
Before starting to load cargo, the responsible officer and the terminal representative must formally agree that both the tanker and the terminal are ready to do so safely.
Emergency plan
An emergency shutdown procedure including contact methods and alarm should be agreed between the ship and the terminal and recorded in writing.
The agreement should designate the circumstances in which operations may have to be stopped immediately.
Due regard should be given to the possible dangers associated with any emergency shutdown procedure.
Watch keeping
The following safeguards must be maintained throughout loading:
- A responsible officer must be on watch and sufficient crew on board to deal with the operation and security of the tanker.
- A continuous watch on deck must be maintained.
- The agreed ship to shore communications system must be maintained in good working order.
- At the commencement of loading, and at each change of watch, the responsible officer and the terminal representative must each confirm that the communications system for the control of loading is understood by them and by personnel on watch and on duty.
- The stand-by requirements for the normal stopping of shore pumps on completion of loading, and the emergency stop system for both the tanker and terminal, must be fully understood by all personnel concerned.
- Emergency stops to trip the cargo pumps are generally provided on port and starboard sides of the manifolds, at the pump room entrance, inside the pump room near the pumps and at the cargo control room.
Loading
Commencement of loading
When all necessary tanker valves in the loading system are open, and the ship has signalled its readiness, loading can commence. The initial flow is generally by gravity, at slow rate and to a single tank. The shore pumps are started when the ship advises that cargo is being received in the correct tanks. When the pumps have been started, the ship/shore connections must be checked for oil tightness until the agreed flow rate has been reached.
The venting system must be checked for correct operations in order to avoid excessive pressures in the tanks.
Periodic checks during loading
Throughout loading, the ship should monitor and regularly check all tanks to confirm that cargo is only entering the designated cargo tanks and that there is no escape of cargo into pump rooms or cofferdams, or through sea and overboard discharge valves.
The ship should check tank ullages hourly and calculate a loading rate. Cargo figures and rates should be compared with shore figures to identify any discrepancy. These checks should, include the observations and recording of the shear forces, bending moments, draught, trim and stability. This information should be checked against the required loading plan to see that all safe limits are adhered to and that the loading sequence can be followed, or amended, as necessary. Any discrepancies should be immediately reported to the responsible officer.
The ship should carry out frequent inspections of the main deck and pump room to check for any leaks. Over side areas should likewise be regularly checked. During darkness, where safe and practical, the water around the vessel should be illuminated.
Topping off
The ship should advice the terminal when the final tanks are to be topped off to reduce the loading rate. After topping off individual tanks, master valves should be shut, where possible, to provide two valve segregation of loaded tanks. The ullages of topped off tanks should be checked from time to time to ensure that overflows do not occur as a result of leaking valves or incorrect operations. The number of valves to be closed during the topping off period should be reduced to a minimum.
The tanker should not close all its valves against the flow of oil.
Before topping off operations commence the ship/shore communications system must be tested. Control valves ashore should be closed before finally topping off the last cargo tank and closing its valve.
Checks after loading
After the completion of loading, a responsible officer should check that all valves in the cargo system are closed, that all appropriate tank openings are closed and that pressure/vacuum relief valves are correctly set.
Using inert gas during the voyage
Loss of inert gas pressure is a very normal phenomenon during the loaded voyage of an oil tanker. It can be due to
- Leakage from tank openings
- Tanks have ullage ports, tank openings, sounding pipes etc that may leak.
- Operational requirements (sampling, ullaging, temperature monitoring etc): Tanks may require to be monitored for temperature, ullage, water cuts during the voyage on a regular basis involving opening of these ports.
- Diurnal change of temperature :
Due to the diurnal change of temperature during the voyage the inert gas in the vacant space above the oil will expand in the day time and contract in the night time. The Pressure valves will lift and release the excess pressure into the atmosphere. This could lead to formation of vacuum inside the tanks.
All of the above lead to intake of fresh air into the inerted atmosphere, making the atmosphere unsafe. It is there fore required that a close watch must be kept on the pressure of the inert gas inside the tank and inert gas be topped if necessary. This may be done using the inert gas top up generator (TUG) or the main inert gas plant itself.
Discharging
General
Vessels correctly operating their inert gas systems are considered to be conducting ‘closed’ discharging operations. Discharge should normally take place on inerted vessels with all ullage, sounding and sighting ports closed. The venting system must be checked for correct operations in order to avoid excessive pressures in the tanks.
Inert gas procedures
Ships using an inert gas system must have the system fully operational and producing good quality (i.e. low oxygen content) inert gas at the commencement of discharge. The inert gas system must be fully operational and working satisfactorily throughout the discharge of cargo or deballasting.
Cargo discharge must not be started until:
- All relevant cargo tanks, including slop tanks, are common with the IG main.
- All other cargo tank openings, including vent valves, are securely closed.
- The inert gas main is isolated from the atmosphere.
- The inert gas plant is operating.
- The deck isolating valve is open.
A low but positive inert gas pressure after completion of discharge will permit the draining of the manifold drip tray into a tank and, if required, allow manual dipping of each tank.
Commencement of discharge
Shore valves must be fully open to receiving tanks before the tanker’s manifold valves are opened. This is to avoid back flow of cargo if the shore tanks are elevated above the ships manifold.
Manifold valves should not be opened until the pumps have developed an adequate pressure.
Discharge should start at a slow rate and only be increased to the agreed rate once the shore has confirmed receiving cargo in their tanks.
Periodic checks during discharge
Throughout discharging, the ship should monitor and regularly check all tanks to confirm that cargo is only leaving the designated cargo tanks and that there is no escape of cargo into pump rooms or cofferdams, or through sea and overboard discharge valves.
The ship should check tank ullages hourly and calculate a discharge rate. Cargo figures and rates should be compared with shore figures to identify any discrepancy. These checks should, include the observations and recording of the shear forces, bending moments, draught, trim and stability. This information should be checked against the required discharging plan to see that all safe limits are adhered to and that the discharging sequence can be followed, or amended, as necessary. Any discrepancies should be immediately reported to the responsible officer.
Any drop in pressures or any marked discrepancy between tanker and terminal estimates of quantities could indicate pipeline or hose leaks, particularly in submarine pipelines, and require that cargo operations be stopped until investigations have been made.
The ship should carry out frequent inspections of the deck and pump room to check for any leaks. Over side areas should likewise be regularly checked. During darkness, the water around the vessel should be illuminated.
2 thoughts on “TANKER OPERATIONS”