Oil tanker –
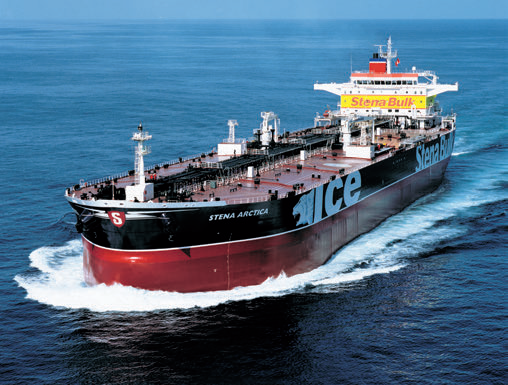
A ship constructed or adapted primarily to carry oil in bulk in its cargo spaces. This includes combination carrier and any chemical tanker when they carry a cargo or part cargo of oil in bulk. Beam and draft restriction have led to a few preferred sizes of oil tankers:
About 35,000-45,000dwt: Panamax tankers configured for transit through the Panama Canal when loaded to their design draft.

About 70,000-120,000dwt: Aframax tankers.
About 120,000-165,000dwt: Suezmax tankers, they may be arranged for multiple grades (three segregated grades is common).

About 200,000-310,000dwt: Very Large Crude Carriers (VLCC) designed for the carriage of crude oils on longer voyages.
About 310,000-550,000dwt: Ultra Large Crude Carriers (ULCC).

Shuttle tanker – A tanker intended to carry oil from shelf fields not accessible to pipeline systems. This tanker type is designed to operate in conjunction with offshore loading installations such as submerged turret loading (STL) system, a subsurface loading station (UKOLS), floating storage and offloading (FSO) units, floating production, storage and offloading (FPSO) units, or articulated loading platforms (ALP/SPM).
The shuttle tanker is in light condition prior to docking with a loading buoy making conventional thrusters non effective in bad weather and heavy seas. As a result, the vessel might have to wait for several days before it could start loading, which costs time and money. To avoid such operational problems, the shuttle tanker should have good dynamic positioning capabilities: the ability to position itself while docking at a loading buoy, and its ability to maintain that position while loading.
Bulk carrier

A vessel designed to carry dry cargo, loaded into the vessel with no
containment other than that of the ship,s boundaries, as distinguished from the liquid bulk carrier or tanker. Conventional bulk carrier is constructed with a single deck, single skin, double bottom, hopper side tanks and topside tanks in cargo spaces.
Common to all are intensive deployment and aggressive environmental conditions and port handling procedures, factors that contributed to a disturbing number of casualties in the 1980s and 1990s. 116 bulk carriers have been lost and 618 seafarers have died since 1992 till 2002. The toll stimulated a number of remedial initiatives by classification societies and IMO, targeting the structural areas of risk.
Structural failure nevertheless remains a consistent and significant cause of losses – 14 bulkers were lost with 23 fatalities in 2000, the average age of the ship 20.4 years – while the presence of heavy cargoes featured in many of the casualties. In 2001 four bulkers were identified as total losses and 64 crewmembers lost their lives; The CHRISTOPHER and HONGHAE SANYO went down with all hands. To prevent this situation, the International
Association of Classification Societies (IACS) is to introduce the harmonized class notations for bulk carriers:
BC-I, covering design loading conditions for homogeneous light cargo, heavy grain and ballast.
BC-II, vessels designed to carry homogeneous heavy cargo.
BC-III, covering loading conditions for heavy cargo with specified holds empty.
The conventional bulk carrier design, with its single side plating between the upper wing tanks and two lower hopper tanks, exposes its vertical framing to the rigors of fatigue,corrosion and mechanical damages. Even a significant increase in the scantling of these members would not offer as much improvement as would be derived from a doublesided alternative design.
Double side skin design eliminates the exposed, damage-prone transverse framing and its end attachments. They protect against cargo–related corrosion and mechanical damage. They allow for better quality surface preparation and coating application. Most importantly, they create much stiffer side structures, effectively eliminating the flexing or fatiguing of the side frame and shell plating connection as occurs in conventional designs.
Operators of double side skin bulkers also report noticeable operational improvements particularly higher discharge rates, simpler cleaning, faster turnarounds and fewer repairs.
It must also be remembered that double sides, by themselves, will not eliminate the possibility of loss. Attention must also be paid to freeboard requirements, to the reintroduction of raised forecastles, to strength of vents and deck fittings and to the strength and watertight integrity of hatch covers, together with particular attention to maintenance and coatings.
INTERCARGO, subdivides bulk carriers in Handysize, Handymax, Panamax and Capesize according to their deadweight ranges.
Handysize bulk carriers – Bulkers in the 10,000 – 34,999 dwt capacity range capable of carrying either dry bulk cargoes or industrial consignments packed in units (e.g. bags of sugar or flour, metallurgical products, timber).
Handymax bulk carriers – Bulkers in the 35,000-49,999 dwt capacity range.
Panamax bulk carriers – 50,000 – 79,999 dwt bulkers, which can pass through the Panama Canal.
Capesize bulk carriers – 80,000 – 199,000 dwt bulkers, the size of which obliges them to go round the Capes of Good Hope and Horn.
Dunkirk-Max – A new “max” design was presented in “Significant Ships of 2001”, named Dunkirk-Max by the builder CSBC; it was marketed as the largest ship, in terms of deadweight and cubic capacity, to meet the specific limitations of the de Gaulle Lock in the port of Dunkirk, France.
Car carriers
Vessels specially designed for efficient transport of cars (pure car carriers), or variety of cars, trucks, tractors and buses (pure car/truck carriers). Cargo access/transfer equipment of typical car carrier consists of a stern quarter ramp, side ramps, internal ramps with covers and hoistable decks. Vehicles drive directly into the ship and via internal ramp system to various decks.

Longhaul car exports were originally handled by bulk carriers fitted with portable or hinge-away car platforms and loading/discharge performed by ship derricks or cranes. But massive rise in demand for global vehicle movements dictated the creation of purpose designed multi-deck pure car carriers (PCCs) exploiting ro-ro cargo handling system. This type of vessels was developed in the 1950s by Wallenius Line, the pioneer in the carriage
of vehicles by sea. RIGOLETTO and TRAVIATA, both delivered in 1955, were the first ships specially designed to carry cars by adding extra decks. ANIARA was Wallenius Line first car carrying ro-ro. Delivered in 1963 it featured a bow door for the first time.
Tonnage with capacity for over 6000 cars on 12 decks emerged, along with pure car/truck carrier (PCTC) designs offering rolling freight flexibility for many vehicle types: not just cars but trucks, knock-down car units, buses, containers, agricultural and construction machinery, and heavy project cargoes. The success of this new breed of ship and the growth of the trades they serve owe much to the efficiency of ro-ro access/transfer installations in loading, stowing and discharging operations. A typical outfit is based on
a stern quarter ramp/door; side ramps/doors and internal hoistable decks and the major players in cargo handling equipment are MacGREGOR and TTS.
The largest deep-sea car carriers in service can carry up to 8000 car equivalent units (CEU).
General cargo ship

Ship constructed for carrying of general cargo not packed in containers.
A vessel with the GL class notation EQUIPPED FOR CARRIAGE OF CONTAINERS is the General Cargo Ship carrying containers occasionally or as part cargo only, and equipped with the appropriate facilities. Such a vessel can have long holds to accommodate containers of different types and flush type lashing sockets on tank top and walls.
The vessel designed for transport of wide range of commodities such as general cargo, forest products, dry bulk, grain, steel coils and usually
equipped for transport of containers. Such vessels have tank top strengthened for heavy cargo and grab operation. Permissible tank top loading 10-20t/sqm.
A vessel with the GL class notation MULTI-PURPOSE DRY CARGO SHIP is the ship constructed for the carriage of general and bulk cargo.
CHEMICAL TANKERS
Chemical tankers are cargo ships constructed or adapted and used for the carriage of any liquid chemicals in bulk. Chemical tankers are required to comply with the various safety aspects detailed in Part B of SOLAS Chapter VIII, but are additionally required to comply with the mandatory International Bulk Chemical (IBC) Code.

Chemical cargoes can be very dangerous, most of them being flammable and/or toxic, some of them extremely so. The IBC Code defines three types of chemical tankers: ST1, ST2, and ST3.
- ST1 is a chemical tanker intended to transport most dangerous products, which require maximum preventive measures to preclude an escape of such cargo. Accordingly, a type 1 ship should survive the most severe standard of damage stability and its cargo tanks should be located at the maximum prescribed distance onboard from the shell plating.
- ST2 is a chemical tanker intended to transport products requiring significant preventive measures.
- ST3 is a chemical tanker intended to transport products requiring moderate degree of containment to increase survival capability in a damaged condition.
The IBC Code lists, in its fourteen chapters, the requirements that must be satisfied by a ship prior to it being certified as a chemical tanker regardless of the specific cargoes it is intended to carry. Within each chapter the designer is given an option of the level of compliance required. If compliance with the more onerous requirements is chosen, the ship will be more sophisticated and will therefore be able to carry the more hazardous cargoes.
Chapter 15 of the Code contains ‘Special Requirements’ which are cargo specific and which must be complied with only if that specific cargo is to be carried. Chapter 16 addresses aspects, which are the responsibility of the operator, whilst Chapter 17 lists all chemicals considered being suitable for transportation by sea. Chapter 17 also summarizes the minimum requirements pertaining to ship arrangements and equipment, which is required to be complied with for the carriage of each chemical, so listed.
The list is regularly reviewed and updated by the IMO to ensure that it contains all products regularly transported by sea and that the carriage requirements remain pertinent.

The basic requirements, which must be satisfied prior to the carriage of any cargo listed in the IBC Code, relate to the general arrangement of the ship. As with oil tankers, the accommodation and engine room are required to be situated aft of the cargo tanks.
A cofferdam is required at the forward and aft ends of the cargo spaces to further segregate the engine room. Cargoes which, if released into the sea following an accident, would pose a significant hazard to the environment are required to be carried in tanks with no boundary adjacent to the sea – that is, tanks protected by a double skin of hull plating (a longitudinal
bulkhead and inner bottom, in addition to the shell plating). Cargoes posing a minimal threat can be carried adjacent to the ship shell plating – that is, either in the centre or wing tanks.
The ship must be able to withstand predefined deterministic damages to the hull structure without catastrophic loss of stability, buoyancy or cargo. This ‘damage stability’ requirement is once again more onerous for those cargoes posing greater hazards.
The major hazards associated with the safe transportation of liquid chemical cargoes in bulk relate to cargo compatibility, toxicity and flammability. The problem of compatibility of each cargo with the materials used in the construction of the ship and its equipment is significant and the list of cargoes in the IBC Code highlights those cargoes which will react
with specific materials.
Cargoes, which react in a hazardous manner with one another, are not permitted to be carried in adjacent cargo tanks or to use common ventilation or pumping and piping systems. Cargoes, which are water-reactive, are not permitted to be stowed adjacent to the ship hull or to ballast tanks containing seawater. Heat-sensitive cargoes, which may polymerize, decompose, become unstable or evolve gas, must not be loaded in tanks adjacent to cargoes, which require to be heated to maintain pumpability. Tanks containing heat-sensitive cargoes are required to be
fitted with an alarm system, which continuously monitors the cargo temperature.
The risk of cargo spillage during loading, transfer or discharge operations is high. The crew is required to be provided with chemical resistant overalls, boots and gloves. Showers and eyewashers are required to be available on deck so that in the event of an accident involving the crew, water is immediately available.
Antidotes for all cargoes carried must be available on board in accordance with the Medical First Aid Guide produced by the IMO. Many cargoes listed in the Code are toxic and the crew and shore-based personnel involved in cargo operations must be protected from toxic vapors. When carrying toxic cargoes, chemical tankers are required to have additional chemical-resistant suits and self-contained breathing apparatus suitable for use in a toxic environment. All toxic vapours displaced from a cargo tank during loading must be vented directly to shore reception facilities through a vapour return line.
Many cargoes are required by the Code to be carried in a controlled inert atmosphere, either because of their flammability, toxicity or to prevent oxygen from adversely affecting the quality of the cargo. Bottled nitrogen is normally supplied to the ship for this purpose; however, many of the more sophisticated ships have a nitrogen generating plant installed on board. Unlike on oil tankers, exhaust gas from the main engines is insufficiently
clean for use on chemical tankers, and could impair the cargo quality demanded by the shipper. When carrying cargoes, which evolve highly flammable gases, the Code requires that all electrical equipment installed within their vicinity shall be specifically designed for use in hazardous atmospheres.
Cargo tank deck foam and firemain systems are required for fighting fires in the cargo tanks or as a result of cargo spillage. The foam compound used must be compatible with the majority of cargoes carried on the ship and an alcohol-resistant foam compound is normally supplied. When cargoes are carried for which foam or water is unsuitable, an alternative fire extinguishing system using a medium such as dry powder must be supplied.
Most modern chemical tankers do not have a dedicated cargo pump room, and normally fit a deepwell cargo pump directly into each cargo tank. Each pump has its own dedicated piping system and cargo discharge manifold. The main advantage of this system is that it enables a large number of different cargoes to be discharged or loaded without the need for time-consuming pipe flushing between each cargo. The cargo piping is required to be constructed of a material compatible with the cargoes carried. To minimise the risk of cargo leakage, all joints – except those to valves or expansion pieces must be welded.
Combination carrier
A general term applied to ships intended for carriage of both oil and
dry cargoes in bulk. These cargoes are not carried simultaneously, except for oil retained in slop tanks. The design of a combination carrier is similar to a conventional bulk carrier but such a ship is equipped with pipelines, pumps and inert gas plant.
Oil/Bulk/Ore (OBO) carrier – A single-deck ship of double skin construction, with a double bottom, hopper side tanks and topside tanks fitted below the upper deck and intended for the carriage of oil or dry cargoes, including ore, in bulk.
OBO carrier can carry three grades of cargo in seven tanks, all of which are coated with tar epoxy, and fitted with a deepwell pump. These are supplied from power packs driven by individual diesel engines.
Ore/Oil carrier – A single-deck ship having two longitudinal bulkheads and a double bottom throughout the cargo region and intended for carriage of ore cargoes in the centre holds or oil cargoes in the centre holds and wing tanks.
CONTAINER SHIPS
Ships intended exclusively for the carriage of containers and equipped with the appropriate facilities. Such vessels have cellular holds with cell guides attached to bulkheads and container foundations. They can be provided with lift-away hatch covers (the usual solution for bigger vessels), or with folding hatch covers that need more space on deck when open.
Deck containers are carried up to 7-high and secured by system of lashing. The capacity of a container ship is expressed in TEU that is twenty-foot equivalent units.

Originally developed for the U.S. for Puerto Rico trade, the container vessel was slowly emerging in the maritime area in the 1950s. Conversions of existing tonnage preceded the first purpose-built containership the Gateway City designed in 1956/7.
The development in the container market was slow until 1968, when deliveries reached 18 vessels. Ten of them had a capacity of 1000-1500TEU. In 1972, the first vessels with a capacity of more than 3000TEU were delivered from the German HDW shipyard. They were the largest container ships until the delivery in 1980 of 4100TEU NEPTUNE GARNET.
When the size of container ships increased to 4500-5000TEU, it was necessary to exceed the Panama maximum breadth of 32.3m and in 1988 the first post-Panamax container ship was built. In 1996 the REGINA MAERSK with an official capacity of 6600TEU started a new era. The maximum size of container ships has rapidly increased to 7200TEU in 1998, and up to 9600TEU for ships delivered in 2006. Recent years have seen the advent of very large container ships with capacity exceeding 13,000TEU.
Feeders – Very large longhaul vessels have created a parallel need for fast, cost effective vessels as feeders and for regional distribution. Feeder containerships are often geared, their deck cranes facilitate cargo handling in ports with limited infrastructure. Small feeders (below 1000 TEU) are normally applied for short-sea transport. The feeders with capacity
1000-2500 TEU are normally applied for feeding very large vessels, but are also servicing markets and areas where the demand for large container vessels is too low.

Hatchcoverless container ship, also open-top container ship – The concept of the containership without hatch covers developed to reduce turnaround time in port and cargo handling costs by eliminating the need to remove and replace covers, and to fit and remove twistlocks and lashing the deck containers. To prevent flooding, the open-top vessel has the increased freeboard and bilge-pumping system designed with the capacity to cope with the volume of water predicted to enter the open holds during the worst sea conditions and severe tropical storms.
Eliminating the hatch covers allows continuous cell guides to extend from the holds to secure the deck containers. The hatchcoverless concept offers the benefit of safe container stowage without the lashing. Furthermore, the open ship configuration gives considerable advantages with respect to heat disposal from cargo holds.
Panamax container ship – A vessel of no more than 294.3m long and 32.3m wide to cross the Panama Canal. The capacity of such dimensioned vessels has developed a very long way from the 3000TEU of the early 1970s versions, to the 5100TEU intake of optimized Panamax containerships.
Ultra large container ships – The size of container vessels has been dramatically increasing in recent years, exploiting the advantages resulting from the economy of scale. The MAERSK ELBA with beam 48.2m (17 rows in hold and 19 rows on deck) has capacity of 13,100TEU and weights over 43,000t. The CMA CGM MARCO POLO has beam 53.6m and capacity of 16,000TEU.
In June 2013 Maersk Line’s first 18,270TEU Triple-E containership was delivered by the Daewoo Shipbuilding and Marine Engineering shipyard at Okpo. Currently, the largest container vessels on order are of 18,400 TEU in size.

While in the past the selected design speed has been approximately 25 knots and higher, lately the preferred design speed has been reduced to 23-24 knots, and even lover. The dual engine installation of Triple-E vessels is intended to ensure a top speed of 23kts, 2 knots less than that of the 15,500TEU EMMA MAERSK. Despite of the 16% increase in payload,
the power requirement is in the order of 65,000-70,000kW, some 19% less than 80,000kW, single–engine installation in EMMA MAERSK.

FERRIES

The term “ferry” originally described a vessel carrying passengers or cargo on short trips across rivers or harbours or coastwise to inland. The USCG defines a ferry as a vessel, “ having provisions only for deck passengers and/or vehicles operating on a short run on a frequent schedule between two points with the most direct water route offering a public service of
the type normally attributed through a bridge or tunnel”. Ferries nowadays are primarily used to carry passengers and their cars, as well as large numbers of heavy-freight vehicles. The car and cargo capacity of the ferries has grown significantly during the 90’s. The number of ro-ro decks has increased from initially only one to two or even three full height trailer
decks. In addition, many ferries have a lower hold to increase the cargo capacity further on.
Cruise ferry – A ferry with cabin space for all passengers and large public spaces with restaurants, lounges, bars, etc. Cruise ferries operate on overnight routes and some passengers are on a “cruise” and travel back with ferry on the return trip. The ro-ro decks are small and the passenger cars occupy a large part of the ro-ro space.

Double-ended ferry – A shuttle ferry with propellers at both ends, featuring an identical fore and aft body. Double-ended ferries are commonly used on short commuter runs where the time lost while turning around a single-ended ferry at each end of the crossing makes a considerable percentage of the time required for the trip, and, thus, the double-ended ferry can transport more units per hour than a single-ended ferry of the same size.

Fast ferries – Various vessels in the 600 – 1000 dwt capacity range, with a service speed well above 30 knots. Weight minimizing is a major consideration in the design of fast ferries. Most designs favour aluminium wave piercing catamarans or steel monohulls. Propulsion is provided either by diesel engines or by gas turbines. Fast ferries are designed to carry
passengers and a variable mix of cars and freight on shortsea routes (15-250 nautical miles). They operate between dedicated docking systems, including berths, linkspans and terminals. Introducing fast ferries created new reasons for travel and provided a good growth in business for operators.

PaxCar ferries – Ferries with passenger facilities suitable for longer routes. They have a full length superstructure to accommodate the passenger cabins and public spaces. Hoistable car platforms are often installed to increase the deck area for private cars.
RoPax ferries – Ferries with large ro-ro decks and limited passenger facilities. This type often has a lower hold, the main deck and upper deck for ro-ro cargo. The deckhouse is lengthened to accommodate space for passengers. The upper ro-ro deck is then partly covered. Most RoPax ferries have both stern and bow ramps to speed up the loading and unloading.

Gas carrier, gas tanker –
Gas carriers are tankers intended to carry different liquefied gases used for energy purposes (petroleum gases, natural gases), in the chemical industry
(ethylene, vinyl chloride, propylene, etc.) or used as a raw material for making agricultural fertiliser (ammonia).
A most notable characteristic of liquefied gas carriers is being equipped with special cargo handling installations designed to keep gas products in
a liquefied state. The design and operation of liquefied gas carriers is principally governed by the International Gas Carrier Code (IGC Code).

Gas carrier types – Gases can be liquefied by using one of the following methods:
- Pressurization under normal temperature.
- Refrigeration and pressurization.
- Refrigeration under atmospheric temperature.
Ships that carry gas products under state 1 above are referred to as “fully pressurized gas carriers”, while those that carry gas product under state 2 are known as “semi-refrigerated gas carriers”. Those under state 3 above are called “refrigerated gas carriers” and this type is often used in design of large LPG and LNG carriers.
Pressure gas carriers, also fully-pressurized ships – These ships are the simplest of all gas carriers in terms of containment systems and cargo-handling equipment and carry their cargoes at ambient temperature. Independent pressure vessels with a typical design vapour pressure of 17.5 bar are used as cargo tanks (type C tanks). Ships with higher design vapour pressure are in service; 18 bar is quite common – a few ships can accept pressure up to 20 bar. No thermal insulation or a reliquefaction plant is necessary and cargo can be discharged by either pumps or compressors.
Because of their design pressure the tanks are extremely heavy. As a result, fully pressurised ships tend to be small with maximum cargo capacities of about 4000 m3 and they are used to carry primarily LPG and ammonia. See also CNG concept.
Semi-refrigerated gas carriers – Constructed in the size range of 1500 to
30,000 m3, this type of gas carrier evolved as the optimum means of transporting the variety of gases, from LPG and VCM to propylene and butadiene. Today, this type of ship is the most popular amongst operators of “smaller-size” gas carriers. Semi-refrigerated gas tankers use pressure vessel tanks designed for design vapour pressure in the range of 4-8 bar. The tanks are made either from low temperature steels for carriage temperature of –48°C which is suitable for most LPG and chemical gas cargoes, or from special alloyed steels to allow the carriage of ethylene at –104°C.
Fully-refrigerated gas carriers – They can carry cargoes at approximately
atmospheric pressure and are generally designed to transport large quantities of LPG and ammonia. Different cargo containment systems have been used in FR ships. The most widely used arrangement is the independent tanks with single side shell. Type A prismatic freestanding tanks capable of withstanding a maximum design vapour pressure of 0.7
bar are used. A complete secondary barrier is required and the hold spaces must be inerted when carrying flammable cargoes.
Heavy lift ships –
Specialized ships capable of transporting non-standardized heavy cargoes.
They can be subdivided into four main categories: project cargo ships, open deck cargo ships, dock ships, and semi-submersible ships.

As most heavy lift cargoes are unique, the management of those require very careful planning and coordination to the smallest detail. Detailed information on cargo and the location of loading and discharging are studied in the preparation phase, often before even the contract is actually booked.
Many projects demand detailed operation manuals, which must be approved by a client and warranty surveyors. Stowage and lifting plans are all prepared with 2D and 3D CAD systems, whereas complicated lifting situations can be simulated step by step.
Project cargo ships – Relatively small ships, often with a large box-shaped hold, used for carrying small machinery, port equipment, locomotives, knocked down cranes, small boats and yachts.

Open deck cargo ships – Ro-ro type vessels with the superstructure positioned fore.They are designed for transport of large modules, fully-erected container cranes, etc, on a large open cargo deck, accessible with a full width stern ramp.
Dock ships– are characterized by the full-length sidewalls protecting the cargo area. The cargo can be loaded by float-in/float-out by submersing the ship until the dock deck is under water, lift-on/lift-off, using cranes, roll-on/roll-off over the ship stern ramp.

Semi-submersible ships – Vessels that are horizontally submersible until their main deck is under water to a depth of 6 to 14m and large cargoes can be loaded using the float-on/float-off method. In this case, the load must be barge-mounted or able to float itself. The ship itself sinks similarly to a floating dock and the cargo is floated onboard. Typical cargoes are drilling rigs, floating plants, dredging equipment, offshore structures, floating drydocks, other vessels.

Icebreaker –
A vessel used for keeping a navigable passage open through ice. Icebreakers
are grouped in ice classes according to the thickness of the ice to be broken. They are heavily built to withstand the shock of ramming the ice or of running up on it at the bow and breaking it by virtue of their weight. Icebreakers are provided with several propellers, not merely at the stern, but sometimes also in the fore part of the ship. Air-bubbler system becomes a part of the standard equipment of a modern icebreaker.

This process involves the expulsion of compressed air through holes in the lower part of the hull. The ascending bubbles then loose ice pieces reducing the ship resistance through the ice. The thrusters can be used to create a propeller wave, which pushes the broken ice away from the hull and creates a wider channel.
LNG tanker –
A highly-sophisticated gas carrier with very specialized LNG cargo containment system built for transportation of natural gases in bulk. As it is usual with LNG tankers, the cargo is transported at a temperature of -160°C.

One of the main requirement of LNG carriers has been the need to use the boil-off gas from the cargo in the propulsion system. Steam turbine was used as a prime mover and steam was generated by boilers burning oil or boil-off gas, or the combination of both. This type of propulsion is relatively inefficient and expensive to operate compared to diesel engines, especially when challenged by dual-fuel diesel-electric propulsion concept.
The move away from steam turbines to diesel engines is the biggest step since a long time. Today many new LNG carriers on order will be powered either by boil-off gas driving diesel-electric installation, with dual fuel
arrangements for the passage with no gas on board, or large two-stroke diesel engines burning conventional fuel, with their boil-off gas reliquefied on board.
LPG tanker –
A gas carrier built for the transportation of petroleum gases in bulk. LPG
tankers often can carry some other gases such as ammonia, propylene and vinyl chloride.
The cargo list for a LPG carrier specifies what type of cargoes the vessel shall be designed for. Practically all LPG carriers can handle LPG, ammonia, propylene and VCM. For larger gas carriers there is a tendency that some of the cargoes are removed from the cargo list.

Considering the temperature and the pressure needed, the LPG carriers can be divided into three categories: full pressure type, semi-refrigerated type and fully-refrigerated type. Small size ships (less than 4000m3 of cargo capacity) are usually the full pressure type. The semi-refrigerated technique is used for the cargo spaces around 7500m3, and fully-refrigerated technique is intended for the cargo spaces between 10,000m3 and
100,000m3.
Seismic Survey Ship –

A vessel mapping out geological structures in the seabed by firing air
guns transmitting sound waves into the bottom of the sea. The echo of the shot is captured by listening devices/hydrophones being towed behind the vessel. Dedicated seismic survey vessels are highly specialised ships. The working decks are enclosed but typically are open at the stern and at a lower level, have the air gun handling system and storage, and at a higher
level, they have winches and storage reels for streamers. The ship itself must be capable of accurate track and station keeping and the propulsion system must have low radiated noise and minimal propeller induced noise to avoid interference with the survey equipment.
Platform Supply Vessel (PSV) –
The PSV is designed for supplying offshore drilling rigs and production platforms with necessary equipment, stores and drilling consumables. These are typically cement, baryte and bentonite transported as dry powders; drill water; oil or water based liquid mud, methanol and chemicals for specialized operations.

The PSV loads at a shore base. Liquid cargo is carried in double bottom tanks, dry bulk cargoes in special pneumatic pressure tanks, equipment and drill pipes on the aft open deck. At the rig or platform, the liquid and powder cargoes are pumped up or transferred pneumatically while deck cargo is handled by the rig crane.
A typical PSV operating profile shows the vessel spending about 25% of the time in harbour loading and unloading, 40% sailing at a service in the 14-16 knot range and 35 % loading or discharging at sea, often in strong winds, high seas and strong currents.
The greatest dangers to a crewman working on a supply vessel include being washed overboard in bad weather conditions or being harmed – either by the cargo he is handling or by the equipment he is using.
Anchor Handling Tug Supply Vessel (AHTS) –
The AHTS combines a number of functions in a single hull. These include handling the anchors and mooring chains for drilling rigs, towing of rigs and platforms together with subsequent positioning on site, and platform supply duties. The required bollard pull has a powerful influence on the design, since this defines the power need, the propeller size, hull shape and depth aft to give the necessary propeller immersion.

Hull beam and shape shall give good stability, particularly when heavy moorings and anchors are suspended from the stern. Anchor handling requires high power, winch capacity, deck space aft, storage bins for rig chains and auxiliary handling equipment. A stern roller is used to ease the passage of wires and anchors over the stern of the vessel during deploying or weighing of the anchor.
Construction Support Vessels –
Dynamically-positioned Class 3 vessels with large unobstructed deck areas, substantial accommodation capacity and significant surface and subsea heavy lift crane capability, able to support surface and subsea construction and installation projects, as well as inspection, repair and maintenance (IRM) programmes.

Construction Support Vessels are designed to provide tailored solutions and facilitate larger projects that often require such vessels to remain on location for long periods of time.
Diving Support Vessel (DSV) –

A vessel provided with diving equipment and used for underwater work such as the maintenance and inspection of mobile platforms, pipelines and their connections, well-heads, etc. The DSV is fitted with a moonpool – a hole in the middle of the vessel open to the sea – through which divers, remotely-operated vehicles and other equipment is passed to and from the worksite. The DSV shall maintain an almost exact position over the worksite during diving operations. In order to accomplish this, it shall be provided with a DP3 class positioning system.
Inspection Maintenance and Repair (IMR) Vessel –
A dynamically positioned ship-shaped offshore unit provided with equipment for well stimulation or maintenance (e.g. coil tubing). Such vessels are often able to carry out other tasks, such as ROV operations and general supply duties.
ROV Support Vessels –

Dynamically Positioned (DP) Vessels from which ROV operations are conducted. ROV Support Vessels are equipped with computer-controlled, precision, position-keeping capabilities with added redundancy features, such as multiple computers, thrusters and reference systems. Such vessels have additional cabins, mess room facilities and Client offices, to comfortably accommodate the Client’s ROV support crews.
Ro-ro –
Abbreviation for a vessel designed to carry vehicles, so arranged that the vehicles may be loaded and unloaded by being rolled on or off on their own and/or auxiliary wheels, via ramps fitted in the sides, bow or stern of the vessel. A ro-ro vessel has one or more decks either closed or open, not normally subdivided and generally running along the entire length of the ship. In this type of vessel, damage stability becomes critical when large portions of the vessel, such as garages and holds are flooded.

Roll-on/roll-off system was first introduced in 1950s and the first modern oceangoing roro vessel was the twin-screw USNS COMET built in 1958 to carry military vehicles. Ro-ro vessels transport wheel-based cargo or cargo that is loaded with wheel-based equipment, and available cargo space is expressed in lane meters. Typical cargo are vehicles, roll trailers and cassettes with forest products or with single or double stacked containers
Cargo is literally rolled on board ro-ro ships. Sometimes roll trailers and cassettes loaded with cargo are stowed by forklift directly on the ro-ro deck. This is called Sto-Ro handling (Stowable Ro-Ro).
As the efficient cargo handling is most important for ro-ro vessels, these ships have large unrestricted cargo decks without transverse bulkheads. Usually ,the ro-ro cargo is loaded and unloaded over the stern ramp, sometimes as wide as the entire cargo space. Internal ramps or elevators are used to reach the upper and lower cargo decks. For really fast cargo handling, two level ramps can be used. Special ramps on the quay are required to facilitate this.

Many ro-ro vessels operate on short trades with frequent port calls. Most of them are equipped with both thrusters and some have also stern thrusters. Usually, they are fitted with high lift rudders in order to ensure good manoeuvring characteristics also at low speeds.