Why cargo spaces has to be Prepared ??
Care of the cargo starts from cleaning of the cargo spaces and generally preparing such spaces for the receiving the cargo. Each cargo has its own requirement and this needs to be attended to meticulously
Introduction
General cargo is stowed in the holds and specified spaces on ships such as tween decks, lower holds or deep tanks etc. These are normally large areas with cubic capacity of a few hundred cubic meters to a few thousand cubic meters. In the holds, special compartments may be built, such as cargo lockers or magazines for stowage of explosives or special or valuable cargoes. Some ships are adopted for carriage of refrigerated cargoes by fitting insulated compartments.
Prior to loading of any cargo in a compartment, whether it is a container, tank, magazine, reefer or plain hold, the compartment must meet minimum standards to receive cargo including cleanliness. In most cases, an improperly prepared hold may result in heavy damage claims due to damage caused by tainting or contamination of cargo. It is the duty of the cargo officer to have all cargo compartments prepared for receipt of cargo. It is not enough if the cargo space is cleaned. There are many items that must be checked in the cargo hold before the hold could be declared ready to receive cargo.
Procedure for Cleaning Holds
Usually, the ship’s crew clean the holds when the ship is at sea. This is economical, convenient and time saving. The cost of shore labour is exorbitant. Valuable time can be saved if the cleaning of the holds could be done during the voyage to load port provided the weather permits such operation. However, on occasions, such cleaning cannot be undertaken due to adverse weather conditions.
Watch It
At certain ports, the unions of dockside workers do not permit ships crew to clean the holds whilst in port. If ships crew plan to clean the holds in the port, this aspect must be checked.
The process of cleaning is simple and routine unless special problems of cleaning are created by carriage of extremely odorous or dirty cargo, for instance, dry fish, carbon black etc. The equipment needed for cleaning the hatch is:
► One dirt sling. This consists of an ordinary rope net sling, with a canvas lining to prevent dust from falling through
► Two rope slings
► Brooms
► Rope yam
► Cluster lights with lowering rope
Let us clean the upper tween deck first.
► At first, a small area in the upper twin deck is Cleared of all debris.
► An area shall be cleaned for stacking of all clean and usable dunnage. (Dunnage is wooden planks of various sizes, which are laid on floors of the hold. Cargo is loaded on top of the dunnage.)
► The broken and stained dunnage is collected and slung up in the rope slings. All other debris is swept, cleared and placed in the dirt sling.
► The clean and usable dunnage is collected from the hatch, neatly stacked in the space cleared over wooden pieces; normally 10-cm X 10 cm wooden supports called battens. The dunnage so saved can be later used for loading cargo.
► If the ship is in Port or at Sea in an area where garbage or debris cannot be thrown overboard, then all condemned dunnage and debris must be kept on upper deck. Nevertheless, you must make sure that these do not obstruct the passage of crew or longshoremen and cause injury.
► A garbage truck is normally arranged to remove all the debris and dunnage from the ship when the ship is in port.
Washing Of Cargo Hold Internally
Washing of holds may be necessary if the hold has been tainted by previous cargo and in any case if grain or other such sensitive cargo is to be loaded in the hold. Washing must be done only after the hold has been swept clean as per the procedure above. The washing procedure is simple.
► Connect a hose with a nozzle to the fire main (please do not use fire fighting hoses!) and direct a solid stream of water over all surfaces of the hold and towards the drain.
► Prior to washing the hold, it is necessary to check that the bilge suction is working; otherwise, all the water accumulated in the hold may remain there.
► The washing is done with salt water at Sea. It may also need a rinse with fresh water. A period of two or three days should be allowed before accepting cargo in this hold, which has been washed down. If outside atmosphere is dry and a good stream of air is circulated into the hold, the drying process should not take more than a day or so. In case of high humidity outside or heavy rains, the drying process may take several days. Therefore, some planning is necessary before washing down the hold. Some modern vessels have dehumidifying systems, which can get the hold dry in a few hours!
Cleaning of spaces contaminated by odorous cargo
If either the drain wells or any portion of the hold is contaminated by odorous cargo, these spaces can be treated with deodorising agents. Usually, a solution contains 250gms of chloride of lime mixed with 10 litres of fresh water is used. First the drain well or the affected area is washed with a solid stream of fresh water.
Thereafter, the affected area is swabbed down with the chlorate of lime solution. if the odour persists some of the powder can be sprinkled in the area. There is another powerful deodorising agent called “HTH” (High Test Hypochlorate), which also comes in powder form.
A tablespoon of HTH added to a bucket of water and the mixture poured in the bilges is sufficient to deodorise the area. Caution – HTH powder should not be left in the area. If the solution of HTH is very strong, it will, of course, eradicate the odour of previous cargo, but the odour of HTH itself may damage the next cargo!
Here, I recall an interesting and innovative method that was followed to get rid of foul odour on the hold. We had loaded Fishmeal in bulk in a hold of a bulk carrier. After discharge and cleaning of the hold, the odour persisted. To get rid of this odour, coffee sweepings were burnt in the hold with the help of coffee burners. The foul fishmeal stink vanished and hold was filled with nice aroma of coffee.
Inspection of the cargo hold and checks to be carried out
It is not sufficient to clean and wash cargo hold thoroughly. Other items in the hold also need to be inspected and checked to ensure safety of cargo and the vessel. The checks are so important for cargo worthiness and seaworthiness that on satisfactory completion the Chief Officer is required entry to make an entry in the mates logbook to that effect.
The following items are to be inspected and checked while inspecting the hold :-
► Dunnage;
► Cleanliness of drain wells, bilges and strum boxes;
► Bilge suction;
► Non-return valve;
► Hold scuppers;
► Sounding pipes;
► Striking plate;
► Temperature pipes;
► Air pipes;
► Accesses;
► Hold Ladders;
► Hold Lighting;
Dunnage
The main contributing factors of cargo damage are:
► Dampness;
► Contact with steel work of vessel or other cargo;
► Lack of ventilation.
► Crushing damage.
Dunnage consists of wooden planks of various sizes and is spread evenly on top of the tank top or the tween deck. Cargo is thereby separated from the deck and likely water or rust that may be on the deck. Cargo is loaded on top to avoid damage. Many different types of wood and material including mats, gunny cloth and paper can also be used as dunnage. In all cases, the dunnage must be:
● Free from oil, grease or other stain
● Dry
● Free of insects or matter, which can develop maggots
● Not covered with bark, and
● Free of nails.
The main purpose of dunnaging is to
► Protect the cargo from contact with water from the bilges or other sources,
► Protect cargo from moisture or sweat, which condenses on the shipside frames, bulkhead etc.
► Provide ventilation to the cargo;
► Spread out the load evenly;
► Prevent chafing and allow the cargo to be chocked and secured, by filling in broken stowage, i.e., end spaces, which cannot be filled with cargo.
► Prevents cargo from shifting by creating friction with the steel plates.
Important
Always ensure that you have sufficient clean and dry dunnage available.
The usual type of wooden dunnage is about 25 mm. thick, 30 cm. wide and 2 m. long. Two tiers of dunnage are laid for loading of general cargo. This is usually referred to as “double dunnaging”. The bottom tier of the dunnage is so placed that any water that may accumulate in the hold due to sweating, condensation, leakage etc would flow freely to the drain well.
The bottom tier should therefore be laid in fore and aft direction with a slight slant away from the centre, so that the water will flow freely towards the drain well located in the aft corners of the hold. In the older ships where there are side bilges the bottoms tier should be athwartship to enable the water to flow towards the side bilges. The second tier should be laid perpendicular to the bottom tier.
Permanent Dunnage
Tank top sheathings
The tank tops of many general cargo ships may be covered with permanent Wooden sheathing of about 70-mm planking laid on bottom to protect the tanks and the cargo. In such arrangements, a single layer of dunnage only is considered sufficient to protect the cargo from sweat damage, if any and also to provide ventilation to the cargo. Spar ceiling /Cargo battens /Side battens
The spar ceiling which are also called cargo battens or side battens, comprise of portable wooden batten fitted to the inner edges of the ship side frames on suitably fitted cleats so as to form a protective layer. Normally, these battens are made up convenient lengths. of planks of about 3 cm. thick and 15 cm wide. They are arranged horizontally in convenient lengths.
The purpose of these battens is to prevent Packages of cargo from Protruding beyond the inner edges of the frames and then becoming damaged by moisture, which may collect on the side of the ship. The space so formed between the cargo battens and the shipside helps to provide a complete air space around the cargo and thereby improves ventilation. tt also permits any leakage or sweat to drain naturally without coming in contact with cargo. In some vessels, the cargo battens may be fitted vertically throughout the hold and tween decks.
The usual size of these battens is 5 cm x 15 cm and is bolted to iron brackets. This type of fitting results in lessening of broken stowage compared to horizontally fitted battens.
These cargo battens must be checked during discharge of cargo and missing and broken ones replaced immediately. You should inspect and replace the cargo battens during discharging operations, so that the higher battens then would be easily accessible.
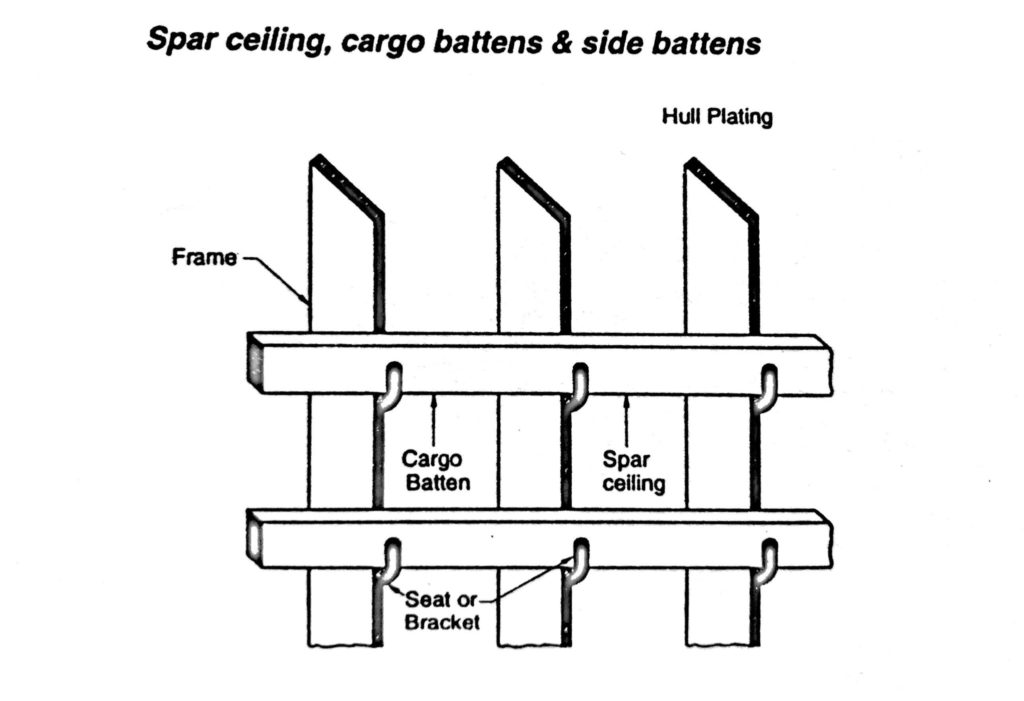
Cargo battens fitted in Roll on Roll off vessels are of larger sizes and serve the purpose of preventing the movement of the cargo, which is of paramount importance. These batten sections are hinged to attachments at the shipside and capable of being pressure forced to the cargo bulk, thus providing an overall tomming effect.
Cleanliness of drain wells, bilges and strum box
The tower holds of the vessel must have an effective drainage system to drain out/pump out water that may accumulate in the hold. The water could be due to sweating of cargo hold or might have come into the hold due to leakage in the hold or drainage into the lower hold from the twin decks through the scupper pipes.
There are two types of drainage systems in the lower holds. In older ships, siad bilge system is followed. In this system, the double bottom stops a few feet inboard to join the hull plating and continues downward at an angle of 45° from the horizontal .
To seal off the bilge system, wooden coverings called mber boards or *bilge boards” are fitted over the face of the bilge. Burlap is spread over these boards and nailed with battens so that bulk cargoes cannot enter the bilges, but water can seep through these boards into the bilges. When a vessel has side bilges, it is important to check all of drainage holes through the bilge bracket where the hull and tank top intersect. The bilge boards or limber boards, which cover the side bilges, need to be removed for inspection. Though this is a time consuming operation, there is no other way to check whether the drainage holes are clear.
In modern ships, system of drain wells is provided where the tank top plating continues outboard in a horizontal plane and connects with the hull plating. A drain well is provided in the aft corners of the hold. The drain well is about 0.2m3 in volume. A perforated plate covers the drain well and this must be kept clean. if the holes get clogged, no water can enter the drain well. This plate must be covered with burlap and sealed with cement prior to loading cargo. This is done to ensure that the cargo does not displace the perforated plate nor allows the cargo to clog the holes.
The liquid that drains into the drain well is pumped out through the bilge pump located in the engine room.
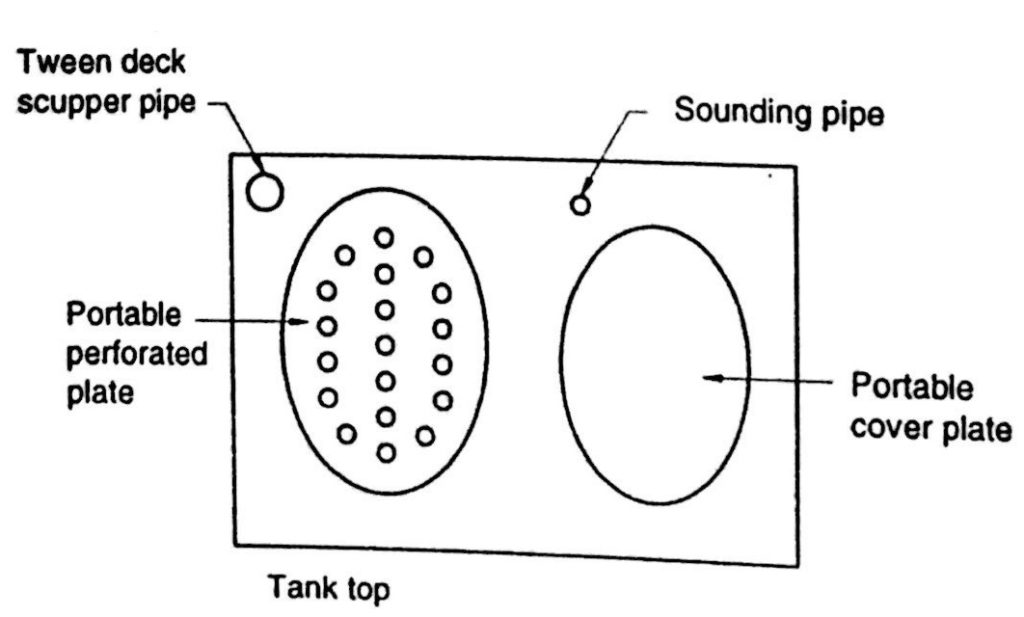
The suction pipe that runs from engine room through duct keel and the double bottom tank enters the drain well. The mouth of this suction pipe is covered with a Portable Cover plate with a strum box, which is a perforated strainer box through which the suction is taken.
The purpose of this strum box or Rose box is to filter any residue or dust so that the suction pipe is not choked or clogged. This strum box or rose box must be removed and inspected. All the holes should be cleared. If the strum box is rusted, it can be replaced. Usually a few of these are carried on board as spare.
Bilge System and Pumping Arrangement
The Bilge main is arranged to drain any watertight compartment other than ballast, oil or water tank and to discharge the contents overboard. In a dry cargo ship the bilge system will be used to remove loose water from;
► Machinery spaces
► Boiler spaces
► Cargo spaces
Bilge system consists of a line termed as BILGE MAIN, passing along one side and around the forward and after ends of the engine room. Branches are arranged from the bilge main.
The number of pumps and their capacity depend upon the size, type and service of the vessel and is governed by:
► Classification Society Rules
► National requirements
► SOLAS requirement of IMO
All bilge suctions must be fitted with suitable strainer/mud boxes.
A schematic diagram shown is a line diagram of a typical bilge suction arrangement where the bilge pump, ballast pump or general service pump can be used for pumping out any bilges.
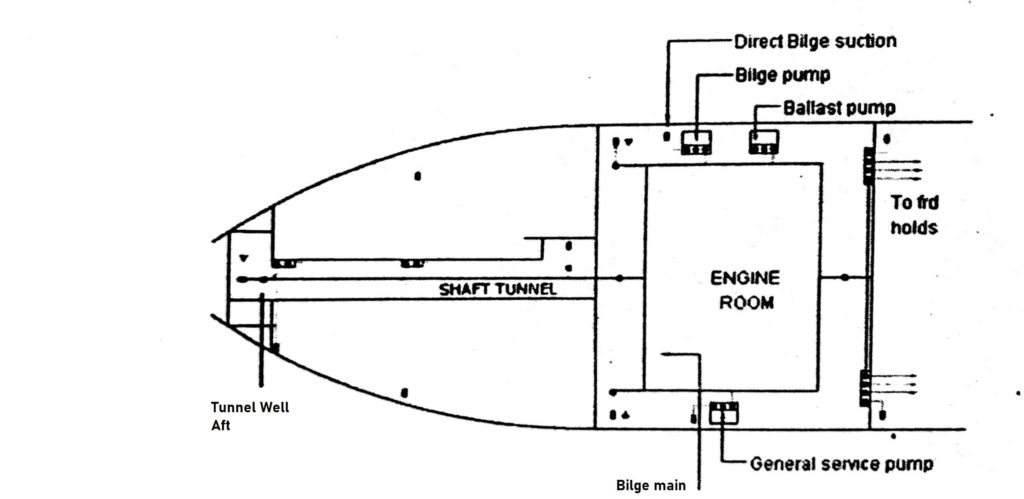
The distribution valve chests are situated in the engine room to enable any bilges to be pumped out by the watch-keeping engineer. All bilge suction valves are of Screw-down non-return type (SDNR) to prevent water flowing back and flooding the bilges, the operating hand wheels are labelled by engraved brass plates as to which bilge the pipe runs into. A mud box is fitted on the bilge suction of each pump and the open end of every bilge pipe in the bilges is enclosed in a strainer box.
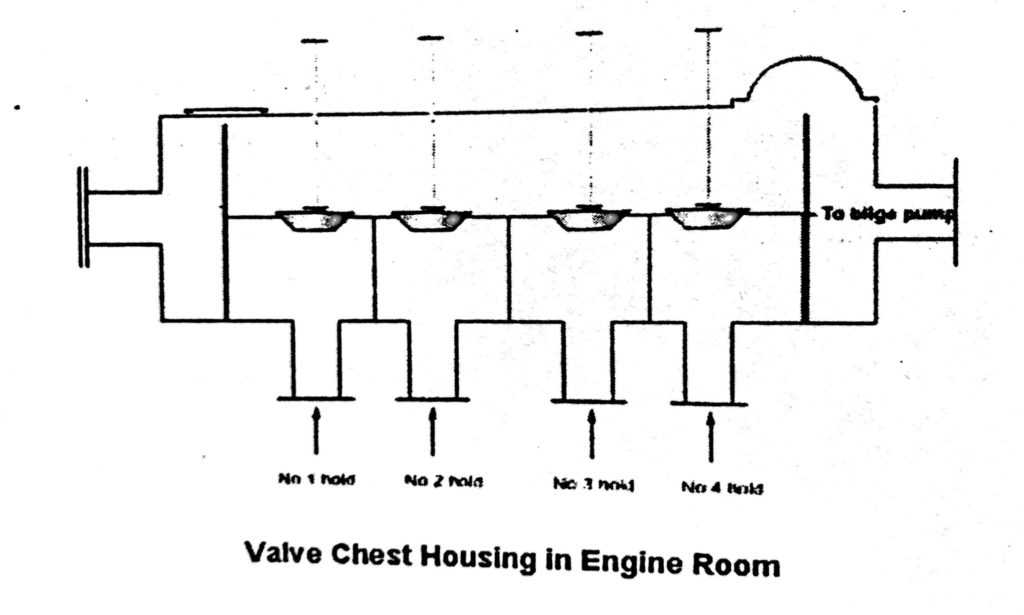
In addition to the above system a special care is taken for the bilge line from Cargo hold bilge wells. A Non-return flap is provided on each line to prevent any back flow to the Cargo hold bilge wells.
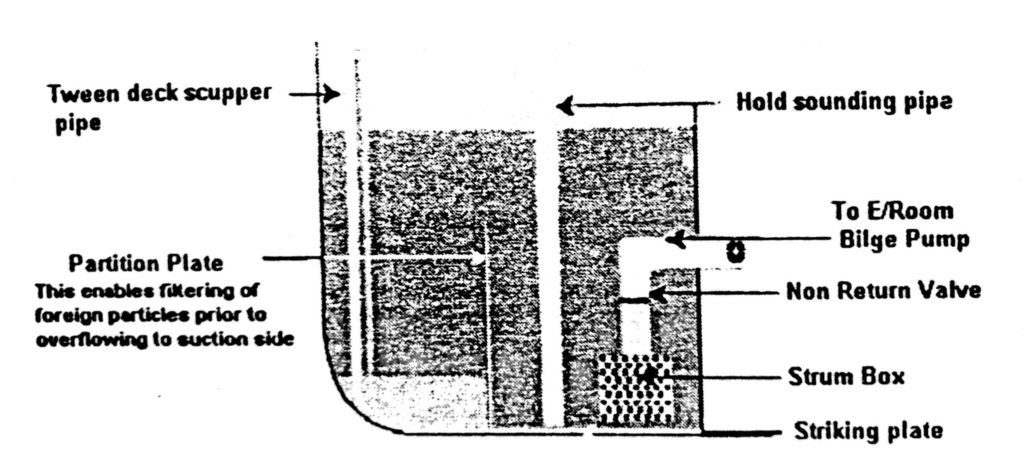
For the deck officer it is very important to certify the Cargo bilges hold bilge system is functioning in order before commencing loading operation. This can be easily checked by pouring a few buckets of water into the drain well and to request engine room to pump it our. Some times if not operated the system for long time the non return flap gets jammed and requires easing up and overhauling.
Bilge Injection Valve
The emergency bilge suction or bilge injection valve arrangement is used in case of flooding of the engine room. It is direct suction form the machinery space bilge, which is connected to the largest capacity pump or pumps.
In case of major flooding in Engine room, emergency bilge injection valve is opened and main injection valve is shut tight. In this case the main pumps for machinery draws water form Engine room spaces and pumps overboard after circulating through main engine coolers.
Bilge suction and non-return valve in the hold
The water from the drain well is pumped out through a bilge pump located in the engine room. It is important to ensure that liquid or bilge water accumulated in the engine room does not enter the drain well through the suction pipe. To ensure this, the suction pipe is fitted with a non-return flap valve just above the level of the suction foot. The valve, which is accessible in the drain well, has a flap, which will permit only suction of water from the drain well to engine room and outboard. It will not permit flow of any liquid from engine room to drain well. The engine room bilge pumping system is provided with a screw down non-return valve. If this arrangement is not there, then engine room bilge water may enter the hold through the suction pipe flooding the hold. In addition, the oily water from the engine room could contaminate the cargo.
At times, the non-return flap valve may get stuck at open position or may not sit properly due to dirt or debris that might have come from the drain well. Therefore, during inspection, you can open the flange of the valve and check whether flap is moving freely and whether the seating is clear and clean. Therefore, it is extremely important to check whether water from drain well can be pumped out before commencement of loading. This can be easily checked by pouring a few bucket of water into the drain well and to request the engine room to pump it out. As you have already checked the strum box and the non-return valve, there should normally be no difficulty in the operation.
Hold scuppers
You would have noticed scupper pipes that carry water from tween decks to lower hold drain wells. These pipes are at times called drain pipes to drain off all liquids from the upper and lower twin decks to lower hold drain wells. The pipes you would have noticed run from the after corners of the twin decks to the drain wells of the lower hold. The first thing to check is whether the cargo operation has damaged these pipes. If damaged they must be repaired immediately. If there is no visual damage, then the scupper pipe should be checked by pouring water from a bucket down the pipe to see whether the water flows through or not. If the flow is obstructed, the pipe should be cleared either with a ‘sani snake’ or by using a rubber plunger. If the pipe cannot be cleared by these methods, they must be removed and cleared or replaced.
Bilge sounding pipes
To find out the quantity of water in the drain well a sounding pipe leading from upper deck to the drain well is fitted. Soundings are obtained by a graduated metal rod lowered down the pipe till it strikes the drain well or bilge. The rod is coated with chalk before lowering. If any water or liquid is in the bilges or drain well, its presence can be found on the brass rod by examining the wetness of the chalk coating. In addition, a rough idea of the nature of the liquid present in the hold can be assessed.
For instance, if the chalk coating is wet and has turned black, you can check whether oil or oily water is present in the drain well. If the ingress of the water in the hold is substantial then investigation to assess the source may be necessary. It is very important to sound the bilges at least twice a day. Usually •the ship’s •carpenter’ or other assigned person takes the sounding and records it in the sounding book and on some ships also writes it on the sounding board.
As a matter of routine, it is also reported to Chief Officer. If due to any reason water enters the hold, it can be found out at a very early stage by sounding of the bilges. It is therefore essential that sounding pipes should be checked during inspection to ensure that they are not damaged or chocked. The sounding pipes on the upper deck have a closing device in the form of a lid or cap to prevent seawater entering the bilge in bad weather. You must ensure these are in place.
The striking plate
The hold bilges are sounded twice a day. The sounding rod made of metal strikes the bottom plate of the bilges/drain well every time the sounding is taken. This plate thus wears out over a long period. The plate is also affected by corrosion due to constant accumulation of water. The consequential thinning of this plate and the subsequent hole in tank top plating may allow ingress of water or oil from the double bottom. This could cause serious damage to the cargo especially if the double bottom tank is pressed up.
To safeguard the steel plate below the sounding pipe in the drain well, this area is covered with a small doubler plate called “striking plate”. This prevents early thinning of the plates. In fact, all double bottom tanks and other tanks of the vessel have sounding pipes. Such tanks are also provided with similar striking plates under the sounding pipes. During periodic inspections of the tanks, the classification surveyor inspects these plates.
Temperature pipes
Temperature pipes are fitted in the cargo holds to take temperature of certain cargoes, such as coal. These are perforated pipes having access on the upper deck, running into the hold. The thermometer is lowered through the pipe, which has pipe guards built around it to safeguard against damage.
Air Pipes
The double bottom tanks of the vessel have air pipes. When a double bottom tank is being filled with liquid, the air from the tank escapes through this air pipe. in bulk carriers, the air pipes run from upper deck into the double bottom tank passing through the shoulder tanks, which are ballast tanks.
If the air pipe has holes, the seawater from the ballast tanks may enter into the hold. In addition, if the double bottom tank is pressed up (that is fully filled), the water or oil from the double bottom tank will enter the hold through the hole in the air pipe. Therefore, it is important to check these pipes.
The air pipes have gooseneck shaped opening on the main deck. The gooseneck openings-are provided with a closing appliance to ensure that the seawater does not enter the tank in bad weather. However if these closing devices are not opened when the tank is being filled or pumped out the tank may suffer damage due to pressure or suction effect.
Access to hatches
Access doors to the hatches are a very important item. These allow access when the ship is at sea or if you are unable to open the hatches in port due to rainy weather etc. If the hatch opening is located in the mast house and if any of the ‘dogs’ (levers to close the door tight) of the mast house door are difficult to turn, they should be made free.
The rubber packing of the door should be clean and free of oil, grease or paint. The knife-edges against which the rubber packing presses when the door is closed should be clean straight and not jagged.
If the hold is entered from the upper deck through a booby hatch entrance, the rubber packing of the lid should be inspected along with the straight edges on which these packing press in the closed condition. In these types of entrances, the lid of the booby hatch is made tight by turning the butterfly nuts. When tightening the butterfly nuts ensure that all of them are tightened to bring same pressure.
You must carry enough spares for these butterfly nuts, as at times, they are stolen if made of brass. The booby hatch entrance to the hold should have hand railings for support while getting into the ladder leading to the hold. The hand railing and the ladder must be visually inspected every time you use it.
Hold Ladders
All rungs of the ladders leading to tween deck as well as lower hold should be inspected. Missing ones must be immediately replaced / welded.
If the vessel usually calls or is scheduled to call an Australian port, a special type of ladder called Australian ladder is fitted at one end of the hold in bulk carriers. This is because, Australian labour union rules requires that, the shore labour should not climb the entire height of the hold of a bulk carrier at one stretch.
Therefore, an intermediate height a platform is fabricated to enable the shore labour to rest prior to continuing their climb to upper deck. Usually, these ladders are damaged during loading or discharge through grabs. These must be inspected and repaired.
Hold lighting
If the cargo hold does not have sufficient light, the safety of shore labour or crew will be jeopardised. Most modem ships have sufficient lights fitted in the hold. Apart from these, a ‘cluster of lights’ or at times called ‘cargo cluster light’ needs to be lowered in the hold to provide additional lighting.
Caution
The ‘cargo cluster light’ should not be lowered on its electrical wire; it should be lowered with a rope attached to it. You must keep a number of clusters of lights ready to lower into the hold.
2 thoughts on “Preparation of Cargo Spaces”